Industrial PC-assisted AGV mobile robot scenario application
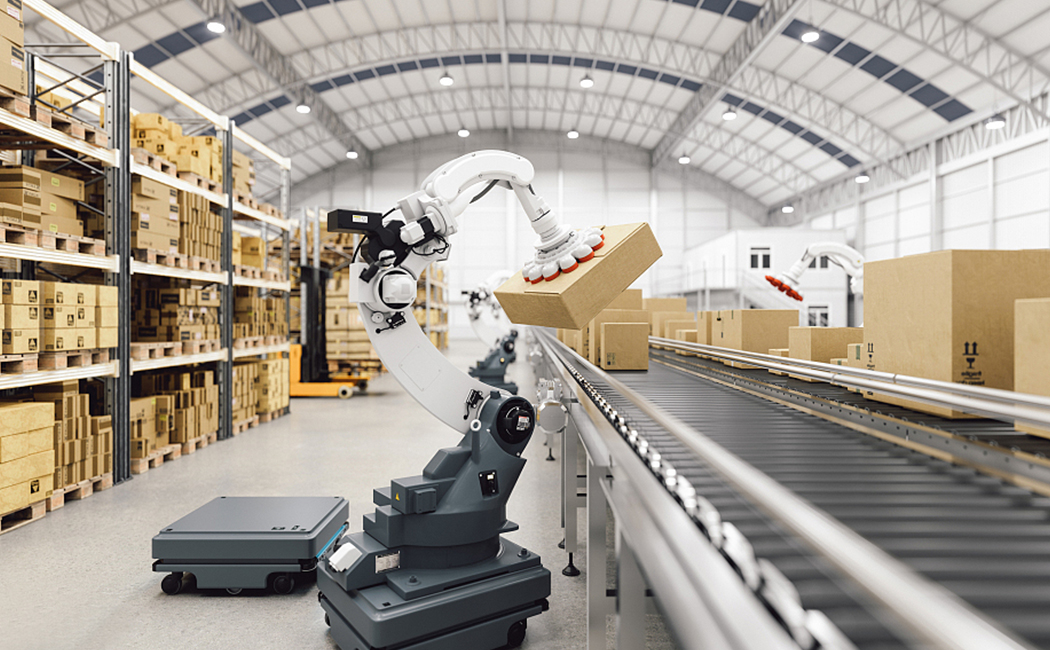
Industry Background: AGV mobile robots are essentially computer-controlled. With the cooperation of electronic control equipment, automatic guidance devices such as electromagnetic or optical, and intelligent industrial control hardware, AGV mobile robots have functions such as autonomous movement, automatic navigation, multi-sensor control, and network interaction. With the help of sensors such as lidar and depth cameras, AGV mobile robots also support functions such as safety identification, automatic obstacle avoidance, intelligent decision-making, and automatic execution. Efficient handling and precise sorting can be achieved without supervision, which maximizes work efficiency and quality in the space. Benefiting from factors such as the reduction of the current demographic dividend, the automation transformation and upgrading of the logistics and transportation industry, and the development of emerging fields, the application scenarios of AGV mobile robots continue to expand, showing good market development potential.
Application Requirements
1.High-Performance
For complex orders in warehousing, picking, shipping, and other processing requirements are huge. There are two laser cameras fixed on the AGV, one on the front for object detection and the other on the center for accurate positioning. A huge warehouse needs to map tens of thousands of locations and have systems track order numbers and individual products on pallets, while wirelessly transmitting the information back to a central control room for collection and monitoring. For these intensive processing tasks, powerful embedded computers with rich interfaces must be used to connect to cameras, motors and wireless networks.
2. Low-Power
AGV need to rest to recharge their batteries, so the longer they are at the charging station, the less time they will work. The computer controlling the embedded must have low power consumption to maximize battery life and then maintain AGV productivity in time between charges.
3. Stability
It puts forward higher requirements for the stability, reliability and environmental adaptability of the main control computer hardware platform in the AGV system, and supports 24-hour continuous and reliable operation.
Solutions And Product: QYT embedded industrial computer EFIC-1000 series, based on Intel 8th Core platform, adopts high-performance, low-power I3/I5/I7 U series processors, which can well meet the response requirements of AGV ground control system; support Gigabit Ethernet/WIFI/3G/4G network, which can meet the barrier-free link of AGV communication; the onboard DDR4 memory supports up to 32G, supports SATA and M.2 storage, and is built in strict accordance with industrial standards, with good electromagnetic compatibility and strong environmental adaptability; fanless design, energy saving and environmental protection, meet storage and 24-hour continuous and reliable operation.
Product Features
1. All aluminum alloy structure, shock resistance, dustproof, high temperature resistance, good electromagnetic compatibility.
2. Intel 8th Core i5 8265U 2.1GHz, fanless configuration.
3. 4 Gigabit Ethernet ports support Wake-on-LAN and PXE boot.
4. COM、USB、GPIO、CAN other I/O optional.
5. Support encrypted onboard TPM2.0 module.
6. Support wide voltage DC 9V~36V power input